Select your pump in less than 2 minutes with the exclusive Expert Tool
Test now our Expert Tool Refrigeration, which offers an expert as well as a fast-track mode. Choose for yourself whether extensive setting options or a pump selection in less than 2 minutes. No matter which refrigerant you are using, it will support you best.
The application grid includes pumping heads up to 180 m, pumping capacities from 1.0 to 85 m3/h, fluid temperatures from –50 °C to +90 °C, power levels from 1 to 19 kW and pressure ratings from 25 to 52 bar. Our widely used pump design tool for refrigeration pumps support you in configure your pump in a simple and fast way.
10 Tips for selecting and designing a pump for use with ammonia and CO2 in the refrigeration industry
1.
Tightness of the pump
2.
Investment and life-cycle costs
3.
Technical design of the pump
4.
Improve the NPSH value
5.
Regulation of the delivery rate
6.
Delivery time
7.
Efficiency
8.
Single-stage vs multi-stage pump
9.
Alignment of suction and pressure nozzles
10.
Pressure rating
1. Tightness of the pump
The toxic effect of ammonia requires the highest standard of safety. However CO2 escape should also be avoided to the extent possible. Canned motor pumps offer the best solution in this regard; motor and hydraulics are designed as a unit in the pump casing and form a hermetically-sealed system.
2. Investment and life-cycle costs
Conventional pumps are not widely used for the pumped media ammonia and CO2. Canned motor pumps statistically show the best MTBF (Mean Time Between Failure) values, as compared to other pumping technologies. Thanks to the low maintenance effort and significantly longer service life, long-term the life-cycle costs of canned motor pumps are lower than they are for other pump types.
3. Technical design of the pump
The most important factor for the technical design of the pump is determination of the operating point (B) based on the plant curve and the Q–H curve (delivery rate and delivery head) of the respective pump. The operating point should ideally be the point of best efficiency. In addition, a reserve is required when designing the drive motor so that motor overload at fluctuating delivery heads are avoided. At motor power of 7.5 kW this equals a reserve of approx. 20 %. HERMETIC offers an innovative, online expert tool for pump design. The expert tools enables plant planners and plant operators to configure pumps with a few clicks. The browser-based software is easy to operate. Based on input of the refrigeration capacity, the circulation factor, and the medium used, it also allows simulation of the pump design in real time and thus optimisation of the design parameters.
4. Improve the NPSH value
When designing a plant, cavitation-free operation must be provided. This is achieved when the NPSH value of the plant is greater than the NPSH value of the pump. If economically justifiable, NPSHA should be selected as large as possible – with a common safety margin of 0.5 m – to prevent possible pump damage. To improve the NPSHR an inducer can be attached directly upstream of the first impeller. The inducer causes an additional admission pressure in the impeller inlet and co-rotation of the fluid to the impeller blade. The inducer is also used preventatively when the resistances and the inflow of the plant cannot be precisely determined. For gas fractions up to 7 % in the fluid the inducer can reliably prevent cavitation. At optimal design of the inducer the NPSH values of the pump can be reduced by almost 50 %.
5. Regulation of the delivery rate
For automatic safeguarding of the pump and for fault-free, cavitation-free operation HERMETIC also recommends installing regulating devices when using CO2 and ammonia. The limits for the minimum and maximum delivery rate (Qmin and Qmax) can be reliably determined with a heat balance calculation and testing of bearing load capacity. A simple Qmin orifice can be used for compliance with the Qmin rate. For maximum pump capacity there are three alternatives: A calculated Qmax orifice, a flow control valve, or a frequency converter with Δp measurement. The Qmax orifice (orifice plate) is installed in the pressure line. It safeguards the delivery rate at initial filling of the plant or at simultaneous opening of multiple consumers. The advantage of the Qmax orifice is the simple and cost-effective design, the disadvantage is the strong throttle effect and associated early drop in the curve (Q–H). The advantage of the flow control valve is a later drop in the curve (Q–H), since throttling only occurs near the maximum rate. The flow rate is regulated by especially shaped openings in a spring-loaded, moveable piston. The flow control valve is mounted on the discharge nozzle of the pump. Use of a frequency converter with Δp measurement (suction-side and pressure-side of the pump) permits regulation at different operating points. The pump capacity can be precisely adjusted to the required refrigeration capacity of the plant. Thus up to 70 % of the energy capacity can be saved, relative to 50 Hz network operation. A real pay-off, especially during continuous operation and long-term use.
6. Delivery time
Whether a new project or assuring operation in the event of pump failure – delivery time is also a crucial criteria, in light of the market dynamics in the refrigeration industry. HERMETIC-Pumpen GmbH has a solution in this area; namely a modular principle that enables delivery of standard pumps within a few weeks and even immediately if there is an emergency. The modular concept enables short-notice adaptation for major or minor change requests.
7. Efficiency
Depending on the refrigerant used, the efficiency of the overall plant and the correlation with the pump used is a hotly debated topic today – even though the pump is only a marginal part of a refrigeration plant. With proper pump design, possible influences on efficiency are negligible. the other hand, the areas of a plant that offer the greatest energy-saving potential are prevention of deposits in narrow piping, avoidance of unfavourable line routing and the compressors. Nevertheless, the pump impeller can be adapted for the highest efficiency of the plant and pump operating point.
8. Single-stage vs. multi-stage pump
Different pumps can be used for ammonia and CO2, depending on the requirements of the overall system. Unlike multi-stage pumps, single-stage pumps only have one impeller. They are primarily used when high pump capacities at low delivery pressures are needed. Thanks to the integrated auxiliary impeller, the HERMETIC single-stage CNF series is also suitable for fluids with a steep temperature-pressure behaviour. On the other hand, thanks to the internal pressure build-up, multi-stage designs offer a great advantage if a low pump capacity with high pressure must be delivered. HERMETIC offers single-stage and multi-stage for all kind of refrigerants. If the operating pressure increases over –10°C, the multi-stage CAMh, which is especially designed for CO2 applications, is used to master the high operating pressure of the natural refrigerant. In addition, the CAM / CAMh series from HERMETIC have an improved NPSH value thanks to the upstream, optimised impeller (see for NPSH improvements point 4).
9. Alignment of suction and pressure nozzles
The alignment of the suction and pressure nozzles depends on the piping and the conditions of the refrigeration plant. Basically two different versions are available on the market: Suction and pressure nozzles attached axially or suction nozzle attached axially and pressure nozzles radially. For the utmost flexibility, particularly when installed in compact plants with low suction head, HERMETIC‘s CAMR series offers radial attachment of suction and pressure nozzles. The pump can be suspended directly under the tank without 90° bends, to save space. For the CAM / CAMh and CNF series the suction nozzle and the pressure nozzle are attached radially.
10. Pressure rating
While pumps for ammonia plants must be suitable for a rated pressure of maximum 40 bar, CO2 imposes higher requirements on compressive strength. In addition, the low viscosity of CO2 must be taken into account. The pump design must be adapted appropriately for the respective pressure rating relative to material composition, casing wall thickness and condition of the plain bearings. The CAMh series, especially developed for CO2 applications, is characterised by a rated pressure of 52 bar and a test pressure of 78 bar. In this regard the operating temperature can be between –50°C and +15°C. Medium can be pumped at delivery rates from 1 m3/h to 14 m3/h up to a delivery head of 85 m. Hydrodynamic plain bearings especially designed for CO2 and low viscosity media minimize the mixed friction, which ensures a long service life and absolute reliability.
Download the 10 tips for pump selection and design now as PDF and you will always have the most important information at hand.
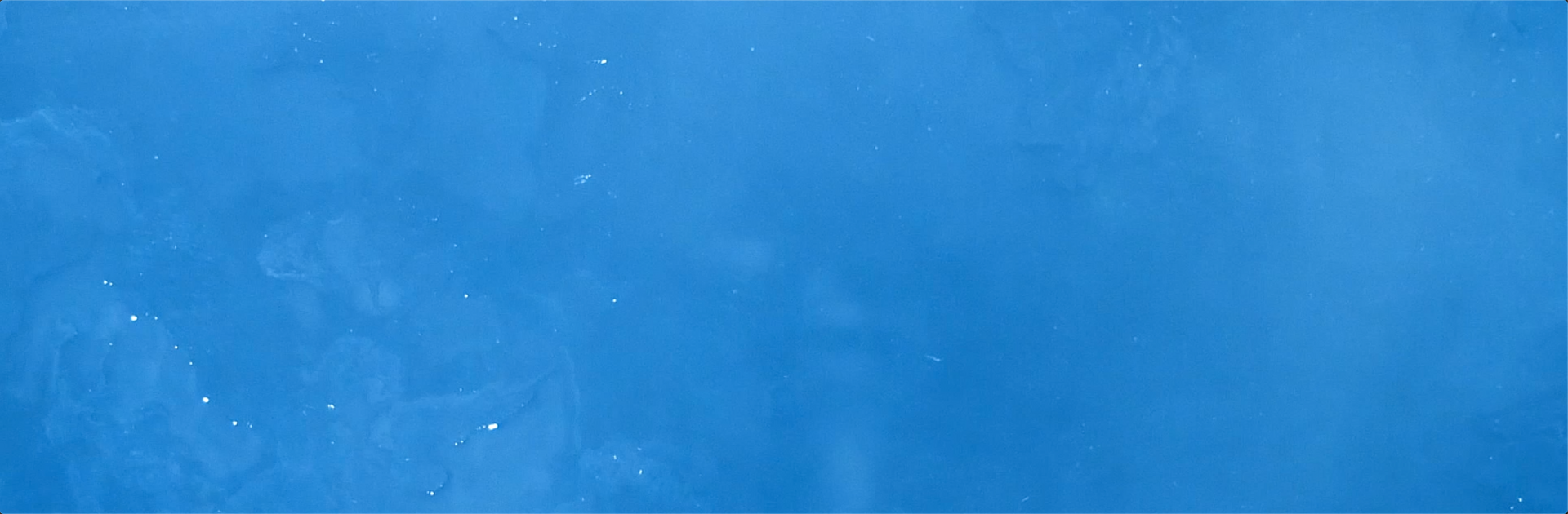